
Last Updated on
By Kip Staton
The art of melting down lead and casting it into projectiles, whether for rifles or handguns, is nearly as old as firearms themselves. And it’s a fascinating subject. Who among us hasn’t thought “Hmm, that’s kind of cool…” while watching Mel Gibson in The Patriot melt down his son’s lead toy soldiers in preparation to take the fight to the British?
If you’re ever in a position in the modern day where melting down toy soldiers is a part of defending yourself from enemies foreign and domestic, things have gone very, very wrong. But that doesn’t mean that you still can’t take advantage of the customization and cost savings that come with “rolling your own” lead projectiles.
Books can (and have been) written about the bullet casting and lead melting processes, but much of the knowledge can only be acquired by heating up some wheel weights and getting your hands dirty. That being said, a large part of the casting process involves preparing the molds and taking care of them during and after the casting session. And the basics of mold prep are quite easily learned about via the printed word.
Mold Materials
Bullet molds are comprised of two mirror-image halves that are connected by a hinged handle (more on handles below). Generally, modern bullet casting molds fall into two primary categories: aluminum and cast iron. Traditionally, cast iron has been favored as the material of choice, due to its ability to be accurately machined and handle heat very well. The downside is that they can be expensive.
More recently, aluminum bullet casting molds have come into vogue, especially when it comes to multi-cavity monsters. Aluminum heats and cools quickly, is cheaper to manufacture and is lightweight. I’ve noticed no practical difference between aluminum and cast iron molds, but some sources claim that aluminum is easier to damage at higher temperatures.
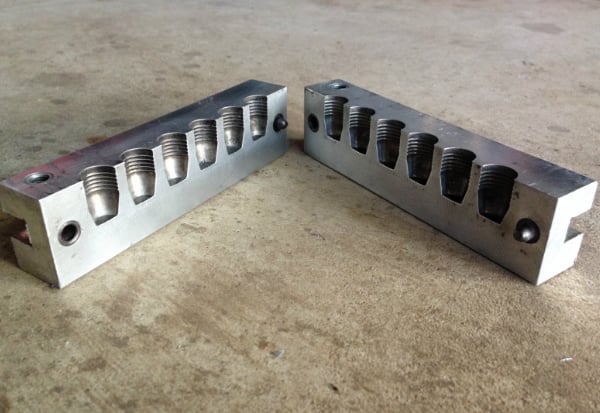
The more bullet cavities your mold has, the faster your rate of production will be. However, the greater inherent mold mass translates to a longer heating period. It can also make your molds quite heavy, which is definitely noticeable during long casting sessions. Thankfully, the properties of aluminum molds mitigate these disadvantages to a degree.
Mold Handles
Obviously, keeping the two halves of your bullet mold together by hand during casting would be foolish and painful. For this reason, all bullet molds are designed to be used with a pair of scissor-like handles, with insulating wooden grips. When you purchase a new mold pattern or caliber, they oftentimes will not include a set of handles, as they are easily swapped out among molds.
For the most part, mold handles are cross-brand compatible. You’ll want to double check before ordering a new mold though, just to make sure.
Maintaining your single set of handles will give you a lifetime of use with every single mold you choose to own, and is very easy to do. Simply ensure that the wooden grips remain firmly tapped in place, as the heat from the molds can loosen them, and keep the hinge point well lubricated with anti-seize grease.
Sprue Plates
In order to form bullets with a perfectly flat and uniform base, molds are equipped with sprue plates. These flat pieces of steel are bolted to the top of the mold faces, and are hinged at one corner. When the hot lead is poured through the holes in the sprue plate and into the cavity, it overflows.
Taking a wooden hammer handle or similar instrument and firmly smacking the impact surface of the sprue plate cuts the soft (but not yet fully hardened) lead off flush with the mold, leaving you with a perfectly flat bullet base each time. Some sprue plates conveniently include a lever to shear the sprue off, eliminating the need for a hammer.
I like to keep the pivot point well-lubricated with a dab of anti-seize grease, just to keep things moving smoothly.
Keeping the lead flowing for slightly longer than necessary will actually connect all of the overflow points into a strip, which makes it easy to pick up the entire thing and simply drop it back in the pot. This is far easier than chasing down lots of little sprue pieces.
Mold Indexing Pins
The scissor-like handles used for bullet casting lack the precision in and of themselves to consistently and correctly align both sides of the mold. Because of this, all bullet molds feature indexing pins at either end.
These tapered protrusions fit into corresponding opposite bushings, and lock the halves together perfectly every time. Because of their precise fit, it’s vital to keep them clean and free of lead flashing and debris. Steel wool and a splash of rubbing alcohol, followed up by a dab of anti-seize, are all that’s needed to keep things clean.
Mold Preparation
Preparing your bullet molds for casting isn’t a complex process, but it must be done correctly. Failure to properly prep your molds can cause poor quality castings, and can even potentially ruin the mold!
First, it’s vital to ensure that the mold faces are completely clean and clear of all debris, lead flashing and other random particles. If the mold can’t fully close, bullets will come out oversized and won’t be usable. Odd looking bullets or flashing will be evident in this case, cluing you in to the problem.
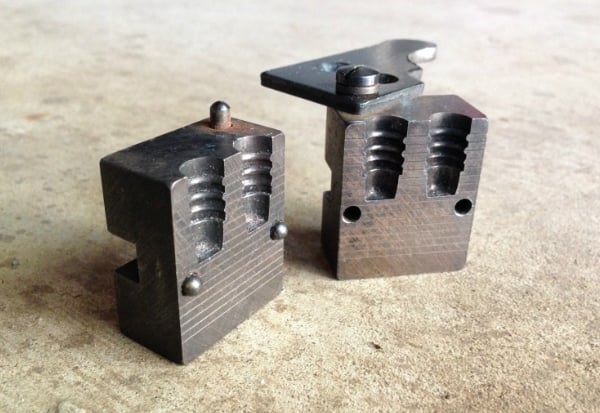
Next, get a match or long-handled lighter. Hold the source of flame beneath each cavity, and “smoke” the surfaces. This places a thin layer of carbon on each mold cavity, and makes it much easier for the bullets to be released with a slight tap on the handles.
Pre-Heating Your Mold
Getting the bullet mold up to the proper casting temperature can be accomplished by letting it sit on the rim of the casting pot for about fifteen to thirty minutes. Pre-heating is important, because the proper temperature will bring the best overall hardness and surface finish to your bullets.
Some old-school casting manuals will tell you to dip a corner of the mold into the molten lead to speed up the heating process, but I’ve found that this is a recipe for disaster and will create more problems than it solves.
When a cool mold hits hot lead, it’s almost assuredly going to unevenly heat things up, have lead stick to it, and just generally be a huge mess. This can also a great way to destroy aluminum molds. Be patient, let the mold sit on the furnace, and let it do its thing.
Let the Casting Begin
When your lead is the right temperature, and your mold has been warming for the prescribed amount of time, you’re ready to get started. The first few cast bullets are likely going to be no good, as the mold needs to finish coming up to the proper temperature.
Since the mold will no longer be sitting on the furnace, it will begin a series of heating and cooling cycles. When molten lead is poured in, this will obviously heat the mold. As the lead cools and hardens within the mold and is released, the mold will then lose heat as it’s moved through the air from the furnace to wherever you’re dropping the bullets.
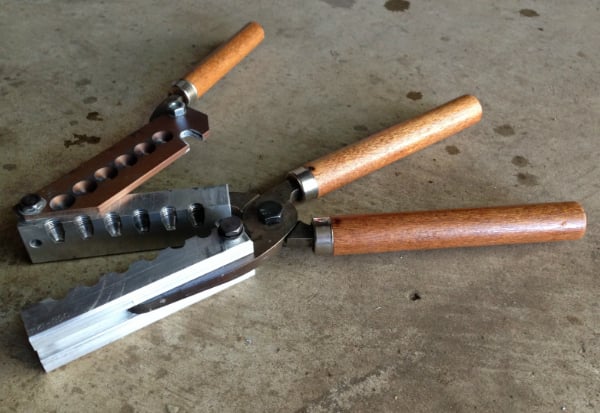
Because of this, your casting cadence is very important. Too brisk a pace, and excess heat will cause frosty, brittle bullets. Too slow, and the cooler mold temperatures will cause wrinkly, undersized bullets. Trial, error and experience will dictate the proper casting rate.
It’s really not too difficult to find and maintain your pace, so experiment and don’t worry if a few bullets aren’t perfect.
After the Last Bullet Drops
Believe me, it’s tempting to just drop the mold on the workbench, call it a day and head inside for a cold drink after an afternoon of casting bullets. You’ll regret it if you just walk away, though. Cleaning up and properly storing your mold after it’s sufficiently cooled off will have you thanking yourself profusely the next time you fire up the furnace.
I usually place the mold in a shaded, out of the way place while I sweep up any sprue strips and generally just tidy up the casting area. By the time these chores are done, the molds are cool enough to clean.
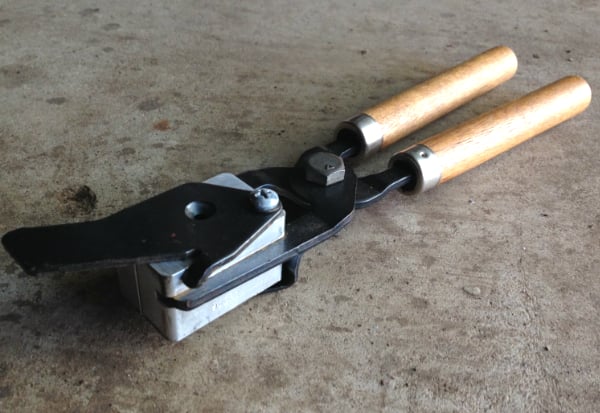
Fully disassemble your mold by unscrewing the sprue plate and removing the handles, if possible. Most mold designs allow for this, but if yours doesn’t, just do you best. Ensure that all lead particles and splashes are removed, and gently scrub down the surfaces with rubbing alcohol and steel wool. Lubricate all joints, indexing pins and hinges with anti-seize grease before storing them in a cool, dry place.
This maintenance routine doesn’t take long to accomplish, but neglecting it can mean starting your next casting session with an unpleasant, rusted mess.
Final Thoughts
It’s important to realize that any experience in casting bullets will (at least initially) have an inherent level of trial and error involved, at every level of the process. But there’s nothing quite like knocking over a hefty steel target or placing well in a pistol match with projectiles that you crafted yourself, from start to finish. Go slowly, enjoy it, and you’ll soon be dropping fresh lead bullets with the best of them.
Leave a Reply